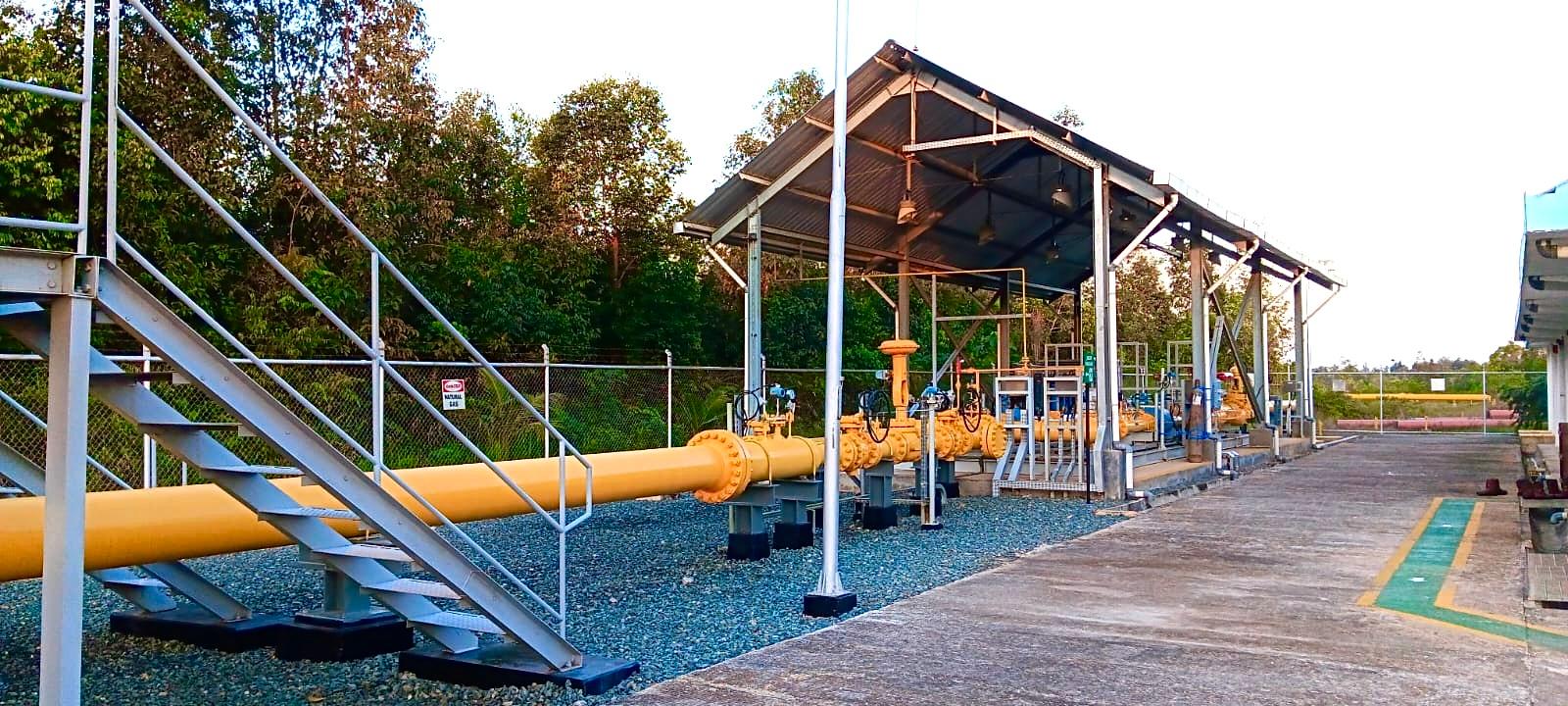
Perfect Balance
Specialty Solution Provider, by prioritizing the perfect balance of EFFICIENT and GREEN solutions.
More About UsEnabling Business Evolution
News
View All News17 Jun 2025
PT National Energy Solutions dan PT Solusi Prisma Metana Menandatangani Perjanjian Jual Beli Gas Alam Cair
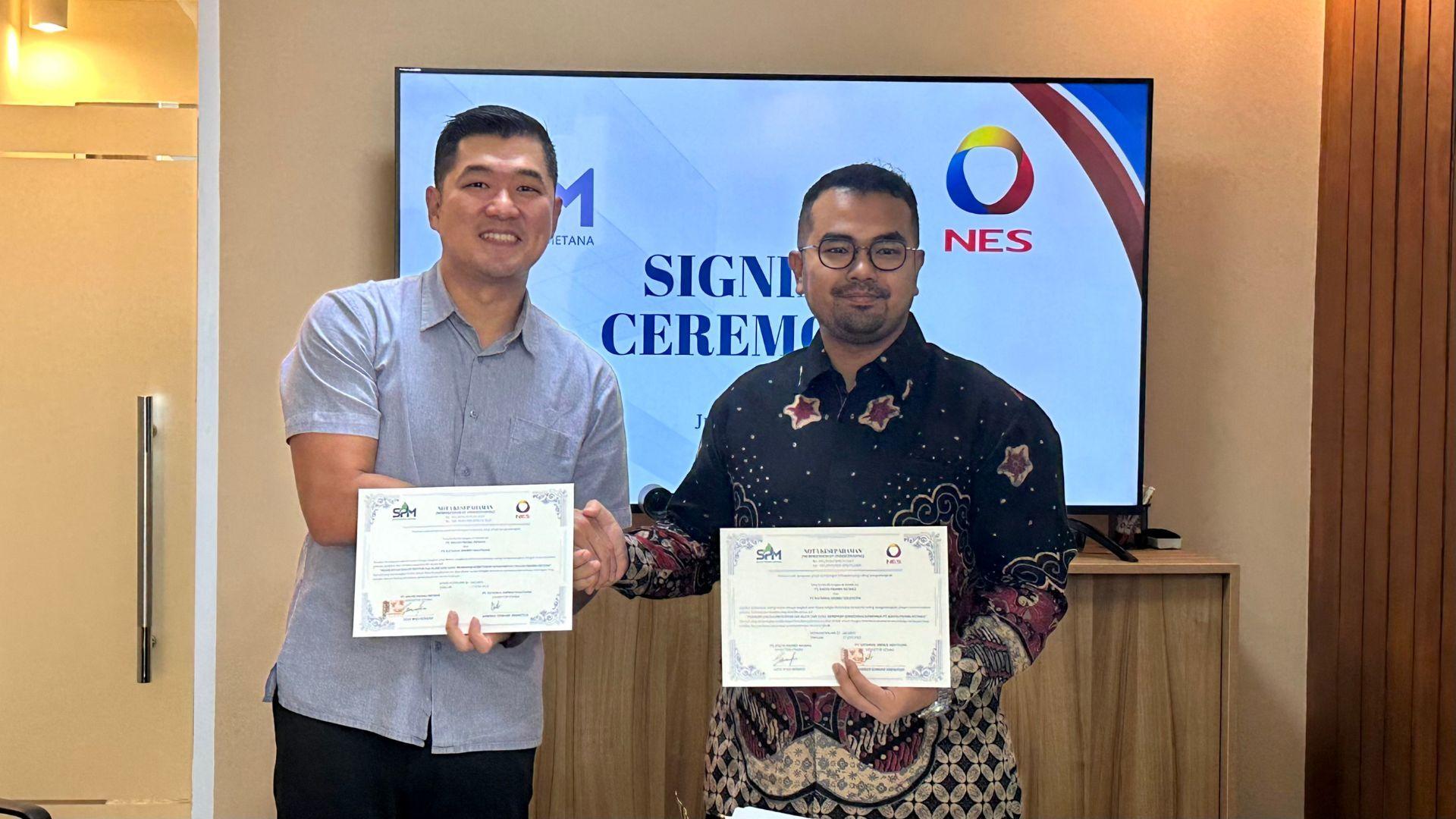
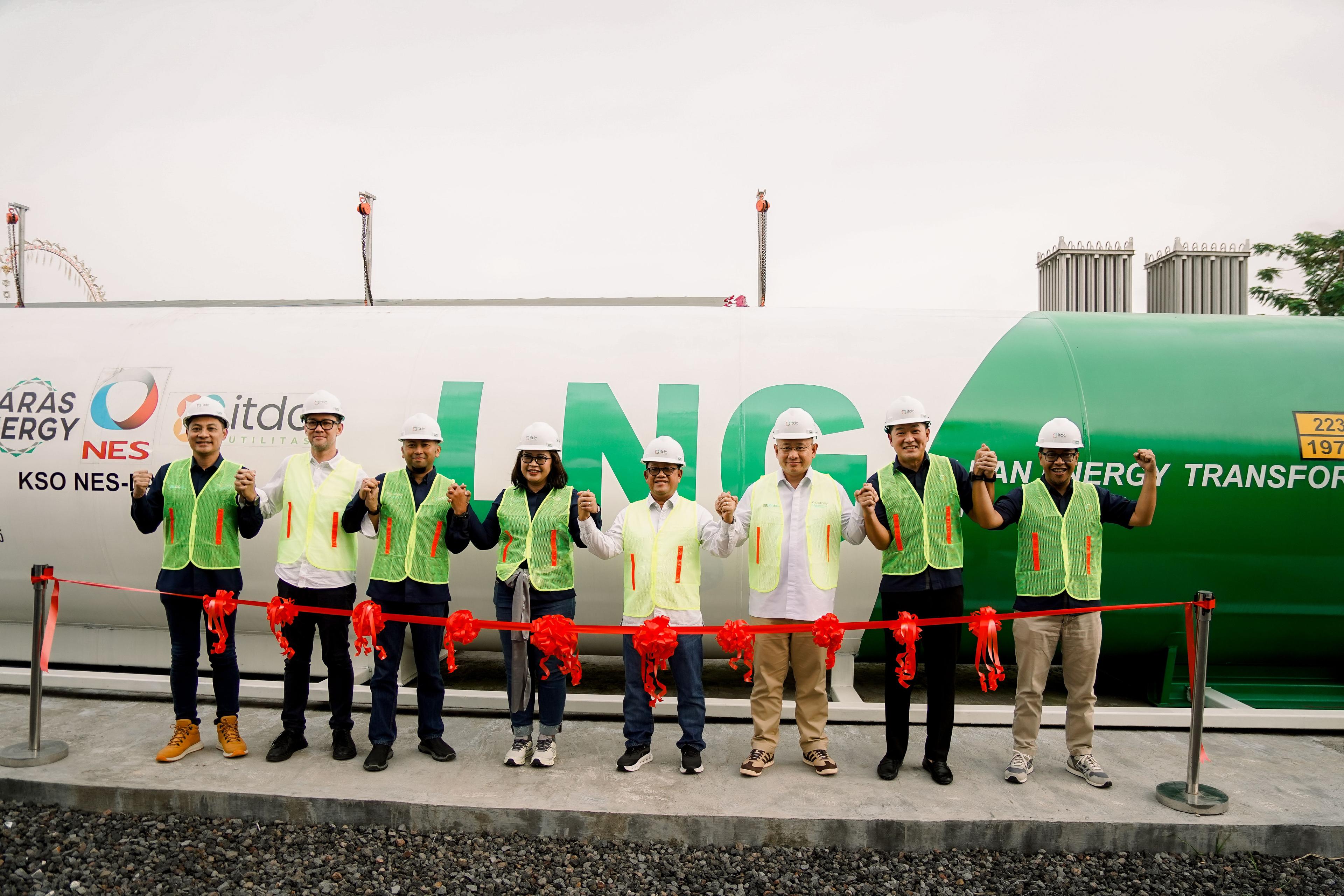
26 Mar 2025
PT National Energy Solutions bersama PT Laras Ngarso Gede dan ITDC Utilitas Gelar Mechanical & Technical Completion Ceremony

26 Mar 2025
PT National Energy Solutions dan PT Laras Ngarso Gede Menandatangani Perjanjian Jual Beli LNG

26 Mar 2025
PT National Energy Solutions dan PT Nusa Energi Sejati Jalin Kerja Sama Pembangunan Mini LNG Plant di Berau
Gallery
View All GalleryNES Group Operation
We explore kinds of business lines such as Coating, Energy, Facility & Outsourcing, Property, Hospitality & Sports, Insurance, Investment, and Procurement.
30Projects
50Cities
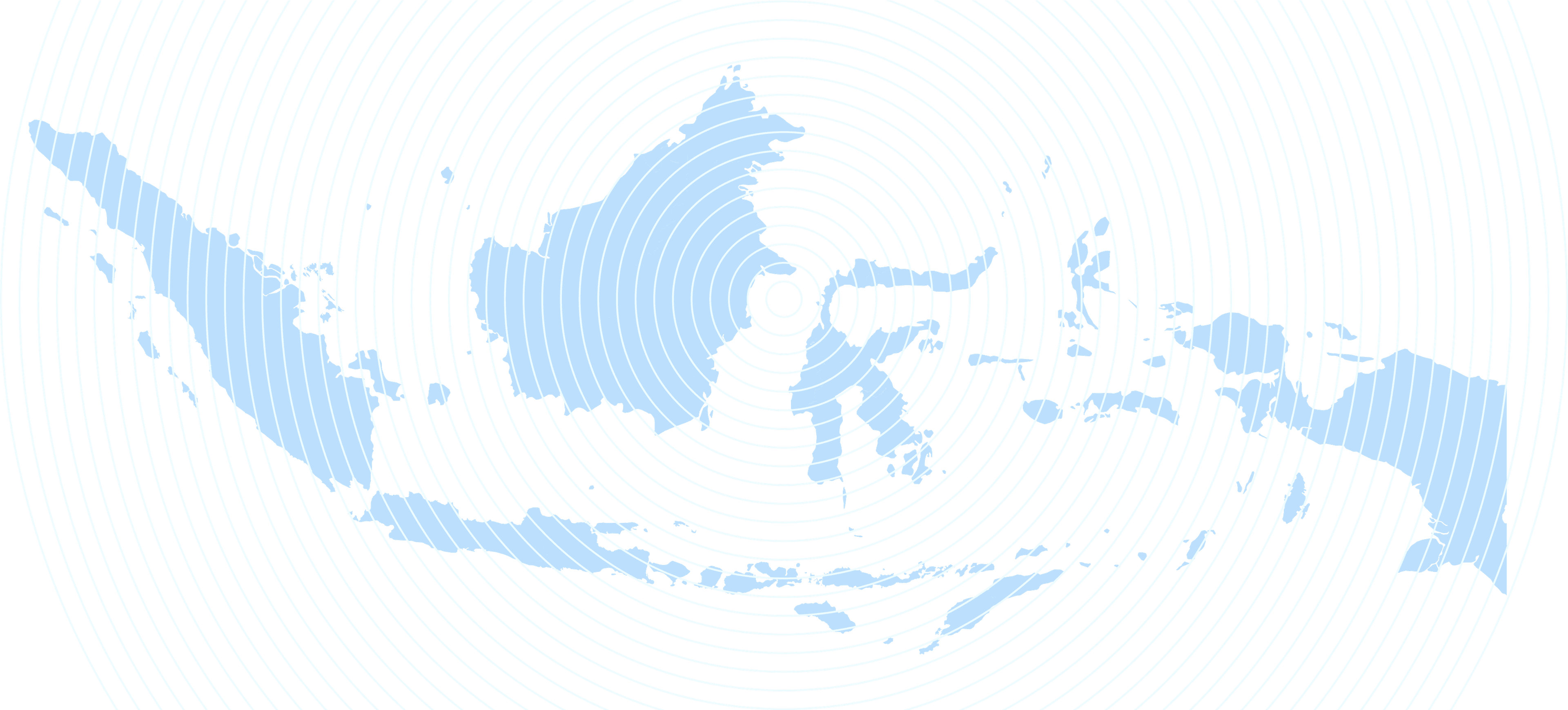
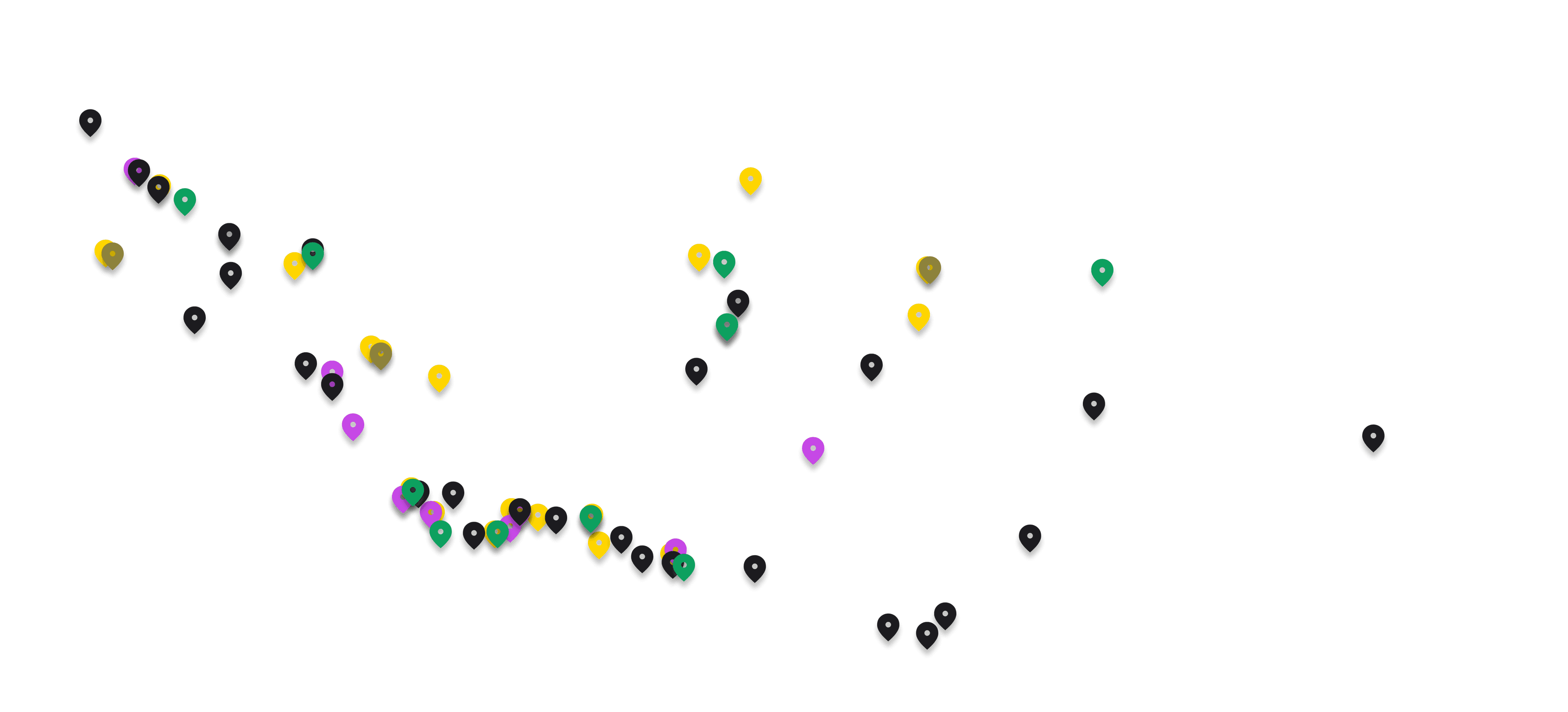